The Crafting
- Vaibhav Shinde
- Jan 26, 2023
- 2 min read
We advanced for the crafting part with fully portable grab bars. In crafting, the final concept is further refined against various criteria like use of material and manufacturing limitations. The final product design is showcased by creating small scale mock-up models, CAD models or working prototypes. The final product which meets the product brief conditions is then taken up for mass production.
We have decided the materials used to make the product based on these factors:
Weight: Heavy weight equals high cost. Maintenance costs, logistics, installation – all see significant cost reductions with a decreased part weight. This is determined by Specific Gravity which is a dimensionless unit defined as the ratio of density of the material to the density of water at a specified temperature.
Strength-to-weight ratio: It is also known as Specific Strength. It is material’s strength (force per unit area at failure) divided by its density. With the advances in plastic composites and the addition of carbon fiber or other glass fibers to plastic material formulations, thermoplastic products can perform as well as and in some cases even outperform metal in ratios such as strength-to-weight.
Strength-to-Stiffness Ratio: It is also called Specific Modulus. It is material’s property consisting of the elastic modulus per mass density of a material. Thus, ABS has greater specific modulus than stainless steel. Hence, it is better.
Production/Lead Time: With a dramatically less labor intensive process, plastic thermoforming can save production time, energy, labor, and cost compared to manufacturing components from metal processes.
Design Capability and Cost: Shaping a metal part can require die work, welding, grinding, rework, or bending on each individual part produced to achieve design specifications and desired look. In addition to greatly increasing production and lead times as mentioned above, as part design complexity increases, part cost increases at an exponential rate.
Thus, ABS plastics is preferred overall for making the body and the covering of suction cups of the fully portable grab bar. For a better grip and comfortability in holding the handle, rubber grips are used.
The CAD models for champion concept i.e., fully portable grab bar are below:

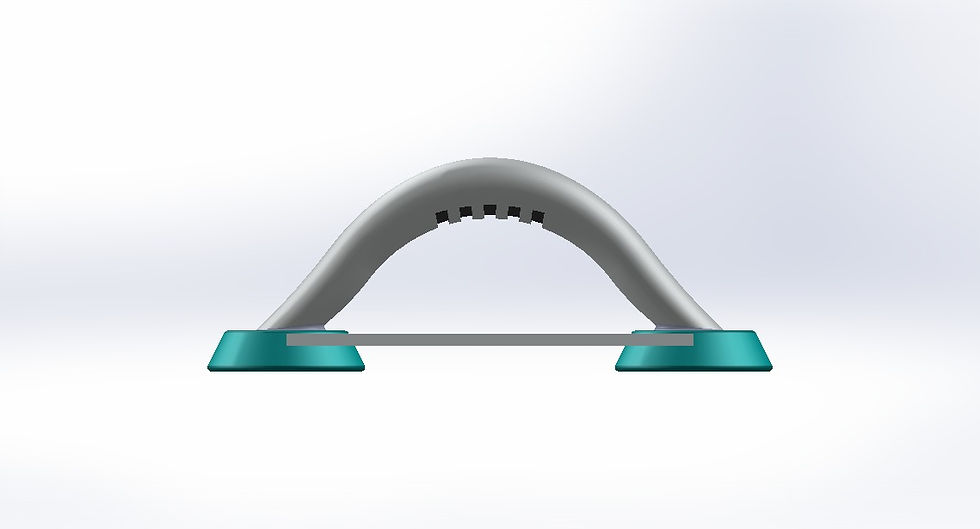


Comments